In the first year of my boilermaking apprenticeship we were required to make our own T-squares, dividers, and other marking off tools and we even made our own ball peen hammer and cold chisels. I've still got the hammer and a couple of chisels I made in the forge shop and despite the fact that I made it, my Firko made hammer is the best balanced of the 10 or so that I own (the hammer is a boilermakers best friend). I've made a shock spring remover almost identical to Fat-Toys, a doo-dad for unscrewing the top of Works Performance shocks that works way better than the factory tool, a few different sized fork seal fitting tools, some dollys for removing dents on pipes and tanks and other gizmos that don't come to mind right now.
It's a real Eureka! moment when a tool you made with your own hands works the way it was intended.
I too did my apprenticeship with one of those companies that made apprentices make all kinds of tools as skill exercises. As a 1st year apprentice Electrical Fitter Mechanic in 1975 I spent my 1st year of “work” in a training workshop run by the company. The company put such an emphasis on the Fitter part of the trade title that the first nine month of that 1st year was spent learning to be a fitter/machinist and doing the same exercises as the Fitter / Machinist apprentices.
Many of the skill exercises were the normal chisel, hacksaw, file type job like turning a piece of round bar into a piece of square bar, but we did make a lot of tools. Some of the better exercises were making your own fabricated steel bench vice and making a boat winch, where you made all the components and had to do all your own welding, and remember we were electrical apprentices.
I still have most of the tools that I made and a few of them are still in regular use. Here is the picture of the most hated tool we had to make;
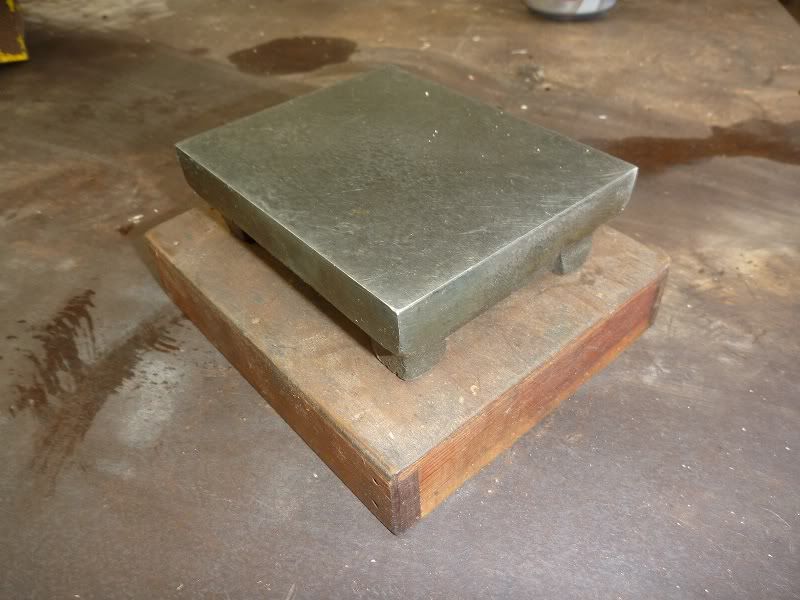
Yes, a tool box sized surface plate! This was one of those things that everyone asked, WHY!
I remember it took me FIVE days to file it square and then scrap the stupid thing PERFECTLY flat. It still lives in my tool cabinet, and surprisingly, although as an apprentice I never thought that I would use it, I do use it to check that the mounting face of flange mount carbies are actually flat and not distorted.
Although a lot us of asked why, and didn’t really enjoy spending days on end filing and scraping etc, I now know that those basic skills I learnt back then have served me very well for the last 37 years and allowed me to make numerous other special tools that I have needed while working on my various bikes.
CJ