Matt if you build a press make sure your bed and top are strong enough, quite often you see where they have bent while pressing and that can cause the job to spit out and be dangerous. You can weld plate on the outside of the bed etc this adds strength and helps to stop bending and also the bed collapsing and spreading.
It is also a good idea to use flat bar for the uprights, this allows you to bend longer lengths in between them where if you use channel you are limited to the width of the press. I machine pressing blocks from dumps of steel and try to keep them if I can to use again later, if you use them once then you will likely use them again.
Try to position the press where you can get to both sides or it it is not to big and heavy then some fit wheels so they can be moved a bit to make this possible. But a warning moving heavy presses can also be dangerous (photo below).
These 1 inch bars bent like they were made of solder when the sling broke while moving it.
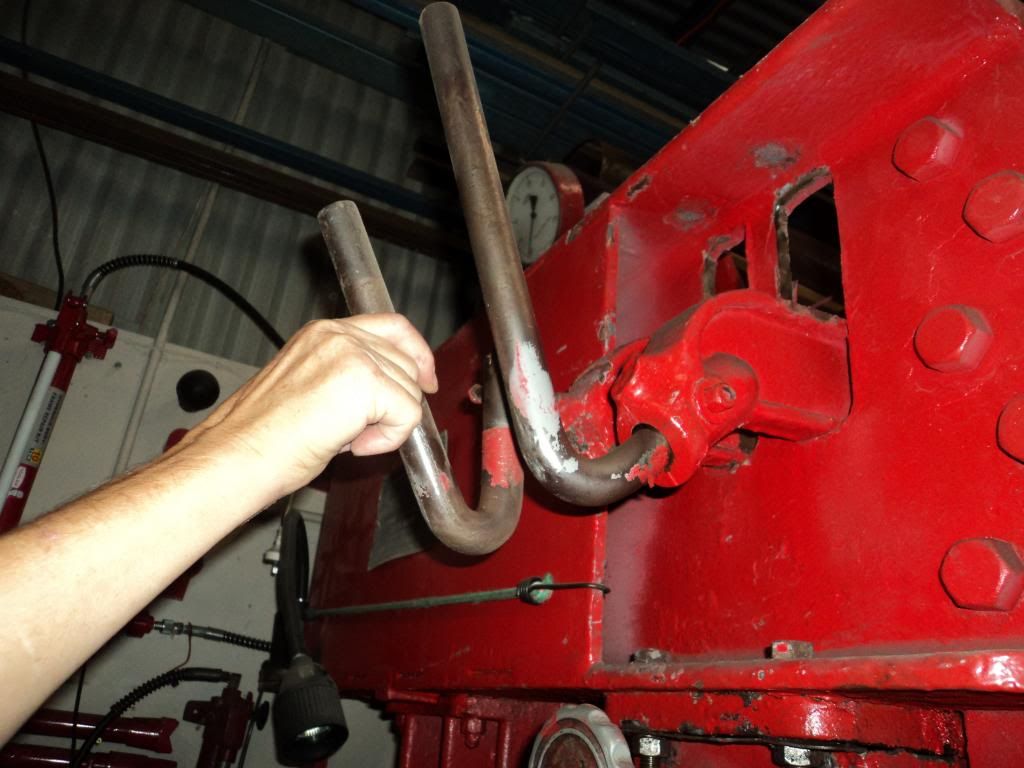
A couple of bits that are handy to have around your press.
I have 3 plates for pushing cranks apart they are made from Bisloy steel and are in 3 different thicknesses for small to large cranks.
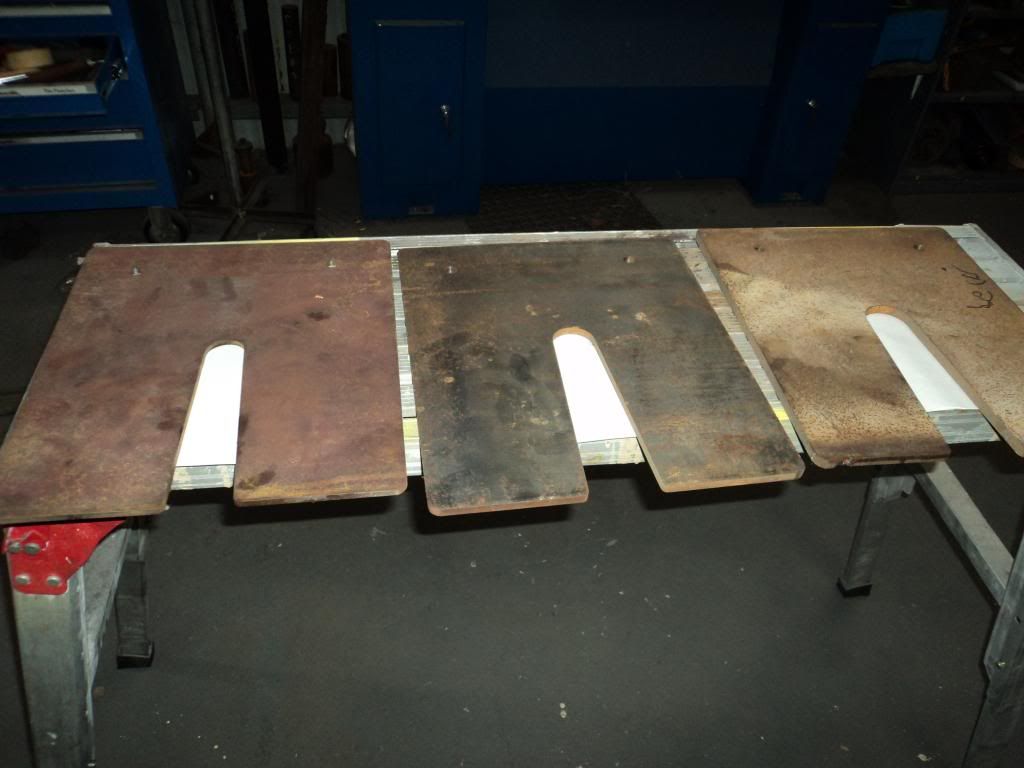
Its handy to have a light, a knife blade for heavy flatbar etc, a light weight knife for folding sheet metal etc, I also made a simple base plate from a bit of flat bar and 2 bits of pipe welded onto it for doing those slow rounded bends.
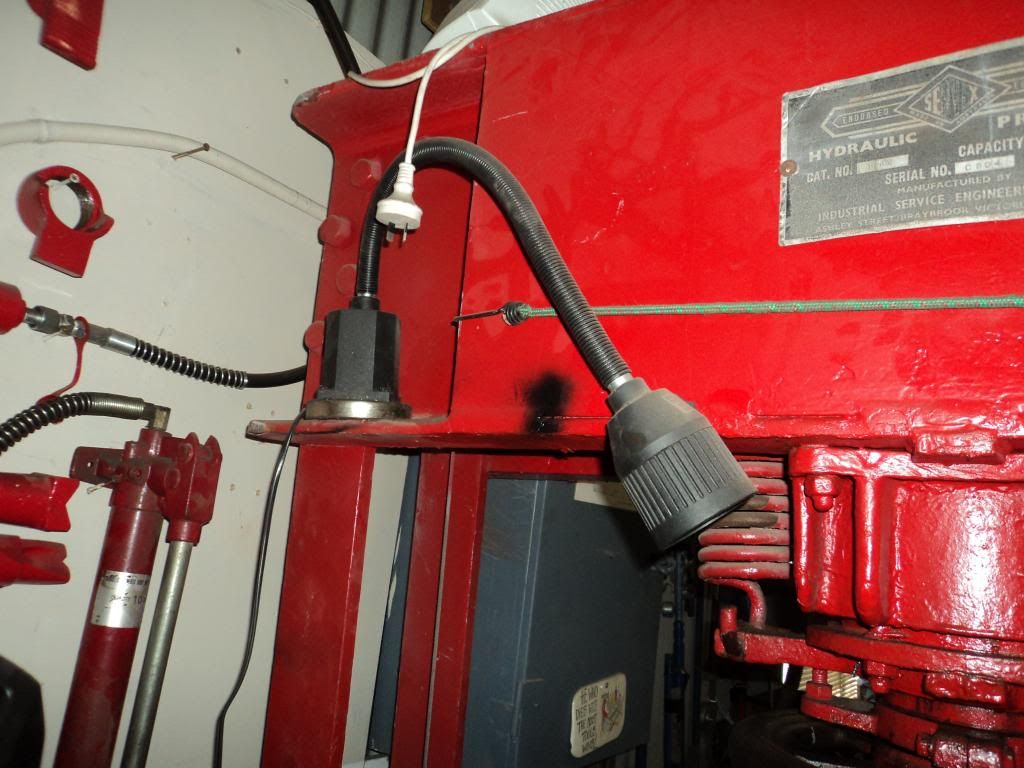
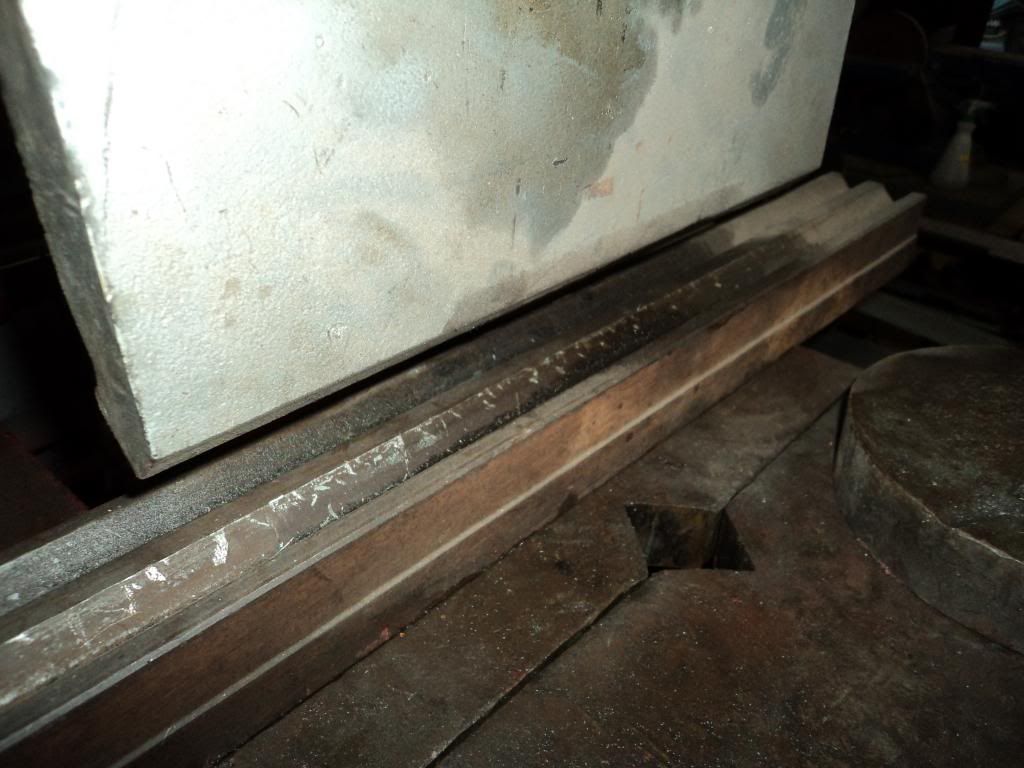
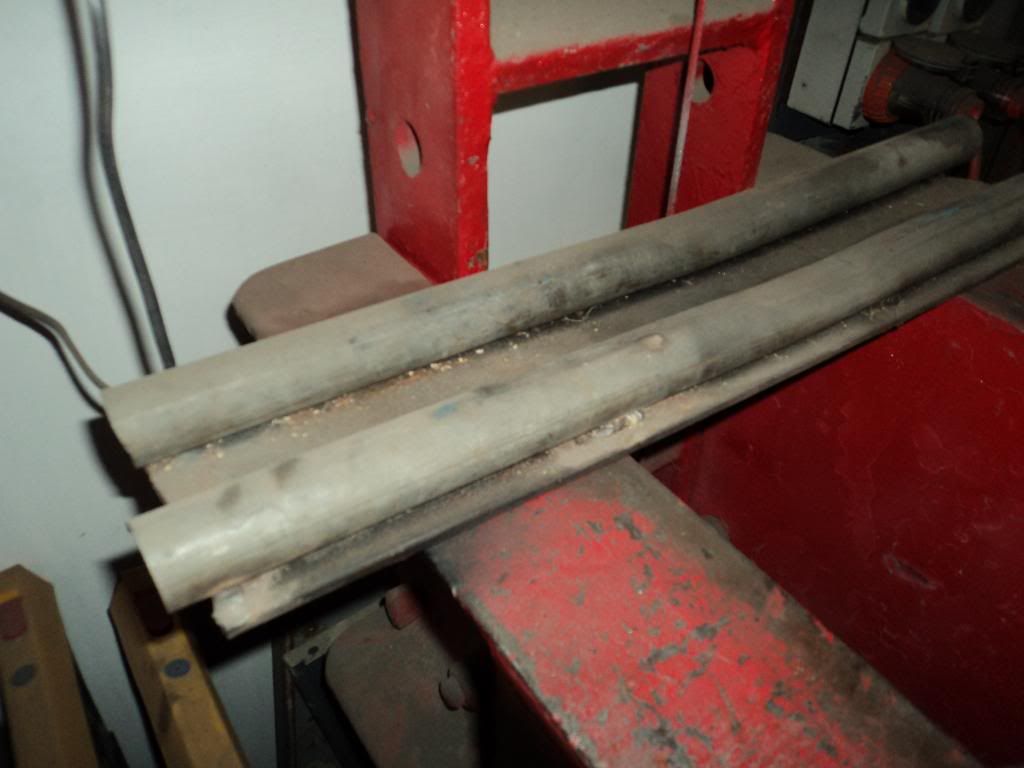
Zane